1、概述
罩极电机是微型单相感应电动机中最简单的一种.由于它具有结构简单,制造方便,成本低廉,运行可靠,过载能力强,维修方便等优点而被广泛地用于各种小功率驱动装置中.其缺点是运行性能和起动性能较差,效率和功率因子较低,一般用于空载或轻载起动的小容量场合,如电风扇等。
2、工作原理
一个没有罩极环仅有主绕组的电机, 是没有起动转矩, 在实际中无法使用, 为了获得起动转矩, 采用附加副绕组的措施。这个绕组不是靠外接电源供电, 而是靠它与主绕组轴线间保待有θ<90的偏角, 见图1。主绕组通电后, 其中一部分主磁通Φm’会穿过这一短路环, 感应电势产生电流, 短路环则如变压器的副绕组一样, 产生去磁通Φk, 与Φm’合成后在罩极区间将是Φs, 最后决定了罩极环上的电势Ek, 这样在主极与罩极的不同区间使有时间相位不同的Φm与Φs在脉振, 构成了椭圆磁场, 产生了起动转矩。在转子是闭路的条件下, 转子就会起动。由于Φm是超前Φs的, 磁场是从超前的磁通移向滞后的, 所以电机的旋转方向是由主极移向罩极的顺时针方向。
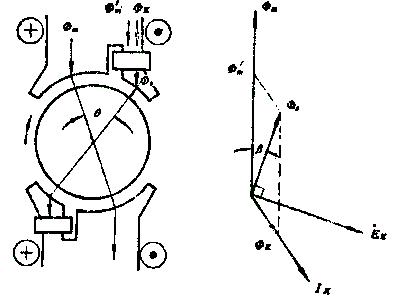
a)工作原理 (b) 矢量图
图1罩极电机的原理及矢量图
3.技术指针及术语
3.1 技术指针
额定功率
额定电压
额定电流
额定转速
3.2 术语
3.2.1效率:电机输出功率与输入功率之比。
3.2.2功率因子COSØ:电机输入有效功率与视在功率之比。
3.2.3起动扭力Tst:电机在额定电压, 额定频率和转子堵住时所产生的扭力。
3.2.4最大扭力Tmax:电机在额定电压, 额定频率和运行温度下,转速不发生突降时所产生的最大转矩。
3.2.5噪音:电动机在空载稳态运行时A计权声功率级dB(A).
3.2.6振动:电动机在空载稳态运行时振动加速度有效值(m/s2)
4.基本结构
罩极电机是结构最简单的一种单相电动机,其结构可分为两类.一是隐极式,从外形来看,定转子均匀开槽,转子为鼠笼式.定子上有主绕组和自行闭路的副绕组或称为罩极绕组.两绕组可以作成等线圈式,也可分别作成正弦绕组.不过两绕组要不成正交的安放,即绕组轴线间夹角小于90度. 它的定子上有主副相两套绕组, 但其主绕组大多采用集中绕组形式, 副绕组则是一个置于局部磁极上的短路线圈, 即罩极线圈(也称短路环).这类电机又可分为两种,一种如图1(b)所示的圆形结构,它的定子可明显的看出凸极型式.主绕组套在磁极上,罩极环则嵌于磁极一角,且多为一个.另一种是方型结构,铁芯如变器一样,见图1(a),主绕组被套于一根铁心柱上,磁极与转子则在铁芯的另一根柱上,在磁极一角多放两个罩环。在罩极电机中, 只要设法产生旋转的气隙磁场, 电机就有自起动能力, 并可正常运转。在罩极电机中, 定子主副相绕组、轴线在空间非正交安置, 并为了改善罩极电机的性能, 采取了各种措施, 如阶梯气隙, 磁桥等, 出现了磁的不对称, 又因副绕组中的电流是靠主绕组感应产生的, 造成了电的不对称, 分别产生时间和空间相位都不相同的磁势, 合成为一个类似旋转磁势的运动磁势, 它在空间建立的运动磁场与转子相互作用, 就可以使之起动和运转。
其结构形式如图2所示:
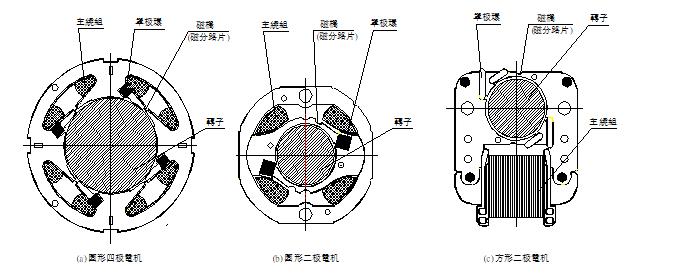
图2 罩极电机的三种典型结构
5.特性分析
5.1 罩极电机效率是偏低的,仅在=(5~30)%之间,因此多用在小功率驱动中.
5.2 罩极电机的主,副相电流变化均不大,故多以电机不动时的电流来计算它的损耗和温升.所以罩极电机会在堵转时运行也不致发生问题.运行可靠是它的最大优点。
5.3 罩极电机的起动和最大转矩倍数规定为T*st=0.3, T*max=1.3, 均属偏小 .因此,罩极电机主要用于对起动转矩要求不高的地方。
5.4 罩极电机经特殊设计,可以在两个方向上旋转.这样的罩极电机磁极在两个极尖上都开有放罩极绕组的槽口.根据需要闭合一个罩极绕组,电机就在那个方向旋转。
5.5 罩极电机可以像单相异步电机那样采用降压或抽头调速.绕组抽头调速的电机,就是在电机的绕组上附加多绕些调速线圈.把这些调速线圈串入回路连于电源上去时,如同电机回路中串入一个电抗一样,达到了降速的目的。
6.结构因素对性能的影响
6.1 磁桥(磁分路)
磁桥的作用是改善气隙的磁通分布,改善电机的机械特性.引入磁桥是故意增大极间漏磁,虽降低了激磁电抗,使激磁电流增大,最大转矩减小,但由于磁桥磁通Φb不与转子匝链,从而增加了主,副绕组的互磁通,使一个极下的气隙磁通由矩形变为梯形,如图3d所示,从而减小了谐波分量。
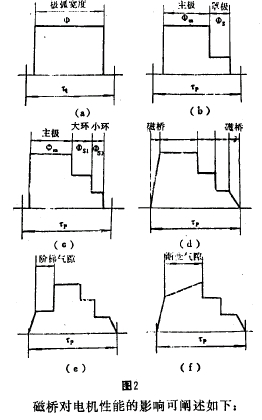

图 3
磁桥对电机性能的影响可阐述如下:
6.1.1转矩转速特性(T-n)曲线
若取消磁桥,电机漏磁减小,使激磁电抗增大,电机的最大转矩Tmax增大.但是,由于此时气隙磁通由梯形变为矩形波,谐波增大,从而谐波转矩分量(主要是3次)增大,使电机在中低速区的T减小并产生明显的凹下.若磁桥太宽,造成漏磁太大,使激磁电抗降低过多,虽然谐波小了,T-n曲线趋于平滑,但根据磁通连续性定理,气隙磁通必然减小,不但Tmax下降过多,而且也导致Tst减小,故亦不可取。
6.1.2起动转矩Tst
当磁桥宽度从0增加时,Tst先是较快增大,过最大值(此时应为最佳宽度)后逐渐下降.合适的磁桥宽度可使Tst增大到无磁桥时的1.2~1.5倍。
由此可见,磁桥宽度是重要的.为了既能改善磁桥磁势波形,又不致使转矩下跌过多,磁桥设计时总使其处于磁密过饱和状态.一般取磁桥磁密在2.2T以上,以限制它的过度漏磁.为此,在初始设计中可如下取值: 在图2a中,为保持一定刚度,磁分路片不能太薄,故可减小其轴向长度,可取铁芯迭长的1/2~1/3.在图2b,c中,两凸极由极尖相连而成一体,为保证机械强度,显然极尖宽度不能太小,故用作磁桥是不行的.为此应在靠近交轴线处的外侧冲制对称的两个半园凹口,以其剩下的宽度作为磁桥宽度.一般取原宽度之半,因为从幅值看可简单认为每极磁通在整个极中分布均匀,即极内磁密处处相等,而凸极中磁密总在1.1~1.5T左右,今磁桥宽度若为极尖宽度的1/2,则磁桥中磁密总在2.2T以上。
图5示出了某8W方形电机磁桥宽度对机械特性的影响。
6.2 阶梯气隙
在前极尖处局部增大气隙,即成阶梯气隙.气隙大了,磁阻就大,由于磁力线总是力图缩短其路径,故阶梯气隙中的磁通密度总是小于主气隙的.从电磁比看,阶梯气隙磁阻与主气隙的磁阻相并联,磁阻(电阻)大者磁通(电流)小.因此,阶梯气隙的采用使一个极下的气隙磁通由矩形波变为阶梯波,如图3e所示,从而减小了谐波分量.效果比阶梯气隙还要好的是渐变气隙,由于从前极尖开始气隙长度逐渐减小,从而使气隙通波成为斜坡形,如图3f所示。与阶梯气隙起同样作用的还有前极尖处冲制闭合长孔(园形电机)或外侧冲制长凹口(方形电机),用增大局部区间磁阻的办法使该处气隙磁通小于主气隙。但由于渐变气隙难于控制,冲长孔又模具复杂,故实际中已很少采用。
阶梯气隙的作用不光可改善运行性能,而且可增加起动转矩.这也正是磁力线的特征造成的,在阶梯气隙与主气隙交界处,部分磁通从主气隙上的定子出发到达阶梯气隙上的转子,也就是说磁力线向阶梯气隙处扭弯,使路径变长,磁阻增大,而转子则力求以磁路磁阻最小来取向,这样就产生了一个由大气隙向主气隙方向的转矩。由于阶梯气隙位于前极尖处,该转矩与旋转磁场方向是一致的。
阶梯气隙长度δc和宽度(以弧角表示)θc对T-n曲线的影响如下: δc不变θc加大,或θc不变δc加大,两者效果大致相同.当δc(θc)加大时,Tst和Tmax都会增大,而且由于谐波转矩减小的缘故,中速区的凹下减小。但过大的δc(θc)将使Tmax反而减小,并且特性变软,工作点的转差率增大,从而损耗增加,效率降低,不过Tst则比无阶梯气隙时始终要大一些。可见δc和θc的取值是很重要的.根据资料推荐,一般取值荡围在δc/δ=2.5~3.5,θc/θp=0.15~0.20。
6.3 罩极环
罩极环的作用是使定子产生一个旋转磁场脉掁磁通Φ.没有罩极环时,仅由主绕组构成单绕组电机,在气隙中产生一个脉掁磁通Φ, 如图3a, 故而电机非但没有起动能力,而且运行时的正转矩较小.有了罩极环,Φ的一部分Φm穿过主气隙,另一部分Φ1穿过罩极区,从而在环内感生电流。由于罩极环是个感性组件,环内电流产生的磁通恒为阻止Φ1的变化,从而造成了罩极区的合成磁通Φs滞后于主磁通Φm.这样,气隙中就有了二个脉掁磁通Φm和Φs,如图3b。由于Φm和Φs在时间上有一相位差,两轴线在空间又错开一个角度,从而合成一个旋转磁场,产生起动转矩,使电机起动和运转。但是,由于两者的轴线夹角θ小于90°(θ=90°时将感应不出Φs了),相角差也小于90°(因环有电阻),再有Φs又小于Φm,故两者的合成磁场永远是个椭圆.并且由于Φs恒滞后于Φm,故合成磁场的旋转方向总是从主极移向罩极,即电机是不能改变转向的。
6.3.1罩极度
罩极度Ks定义为罩区磁极宽度占整个磁极宽度的百分比,它的大小对电机性能 影响很大.假如两个脉掁磁场的强度相同,则Ks越小,两轴线夹角θ就越接近90°,旋转磁场的椭圆度越小。但是,由于Φs是主绕组感应产生的,Ks越小, Φs越弱,旋转磁场的椭圆度越大.由此可知,势必存在一个最佳的Ks值,它权衡了二个磁场的夹角和幅值,使合成磁场的椭圆度最小。分析与实验表明,单罩环电机的最佳罩极度为33%(即1/3)左右,此时的Tmax和Tst均较大,而且T-n曲线也比较平坦.由实验知道,Ks大时,T-n曲线的中速区凹下很小,但Tst较低。极限Ks=100%时,主副绕组轴线重合,相当于一台短路变压器,副绕组中感生电流最大,这时只能产生脉掁磁场,Tst=0.减小Ks时,Tmax变化很小,Tst先增大,但中速区凹下逐渐变大;小于33%以后,Tst又趋减小,极限Ks=0时,Tst=0。在方形铁芯中,由于结构上的允许,一般采用二个罩环,构成三绕组电机。在三相对称电机中,一个极(180°电角度)中每相各占60°,即60°相带.而双环电机虽不可能实现这种对称分布,但道理是一样的,从而大小环取长补短,电机特性明显比单环好得多:Tmax和Tst均增大,且中速区下凹不严重.实验表明,在双环电机中,当主极取110°左右,大环70°左右,小环则在大环的70°中占40°左右时,电机特性较好.换句话说,一般取大环Ks1=40%,小环Ks2=22%左右。
前面讲过.为了获得大的输出转矩,合成磁场应尽可能接近圆形.为此要求Φm与Φs具备三个条件:强度相等,轴线在空间相差90°电角度以及相位角相差90°.但这是相互矛盾的:由于Φs是主绕组磁通Φ感生的,故主副绕组轴线夹角越近90°,两者的互感应越小,即Φs越弱.在极限位置90°时,主绕组产生的磁通不能穿过副绕组,这时副绕组中就不能感生电流,从而Φs为0,不能产生转矩.为了在较小的罩极度时能产生较大的副相磁通Φs,采用磁桥是完全必要的.由于磁桥的存在,使一小部分磁通不经由气隙-转子-气隙从一个极到达另一个极,而是通过磁桥,也就是说这一小部分磁通是不与转子匝链的是属于漏磁通。这样一来,由于罩极环中的部分磁通不通过气隙,故罩极环部分的磁路磁阻减小,从而环中的磁通Φs增大.也可理解为磁桥增加了主副绕组之间的互感,从而互感通增大。
6.3.2罩环阻抗
罩环的位置确定以后,其本身的参数对电机性能也有很大影响.罩环电阻rs对起动 转矩有一最佳值,rs过大或过小,均会使Tst下降.在通常所见的电机中,一般来说,凡是仅有一匝的粗铜线或扁铜线,rs偏小,而用漆包线绕制的多匝型副绕组则rs偏大.rs偏大时,在空间位置许可的情况下,可尽量换用粗一档线。对rs偏小的电机,若换用黄铜之类的等直径线,电密不变,rs又提高了,是电机性能将改善.罩环漏抗xs的增大将使Tst下降,为此罩环端尽可能紧贴迭片,且其槽应尽量靠近定子内径,以力求减小其漏磁通。
6.3.3罩环的损耗
尽管罩环的匝数少,环内的感应电势很小,但由于其阻抗极小,故环内电流通常是很大的,使损耗很大,温度很高,尤其是在堵转时,可达150°C以上(半导体点温度计).由于罩环是参与运行的,从而使电机的效率很低,也使电机具有在超载甚至堵转时整机电流变化不大,不易发生故障的优点。若电机设计不合理或罩环接头焊接不良,罩环发热将相当严重,甚至可烧断焊点,使电机不能正常工作,因此罩环的焊接质量是绝对不能轻视的。
6.4 主绕组阻抗(电阻r1及漏抗x1)
是主绕组阻抗增大, 其上的压降增大, 由于这是属于无用的消耗, 导致绕组中感应电势降低, 由于感应电势为E1= , 当电源频率f和匝数W1不变时, E1降低, 意味眷每极磁通Φ减小, 从而电机出力减小.增大主绕组电阻r1时, 损耗增加, 输出减小, 温升增加, 但是, 当r1增加时, 并不是输出的减小等于损耗的增加, 而是损耗增量中的一部分由电源输入来补偿, 一部分由输出减小来补偿. 因此, 增小r1( 例如线径减细一档)而不减变匝数时, 对固定负载而言, 电机的输入增大, 输出略有减小, 转速有所降低, 功率因子则略有上升, 温升明显上升. 对风叶类活动负载而言, 由于其功耗基本上与转速的三次方成正比, 转速稍减时, 所需转距下跌很多, 故电机表现为输入减小, 输出略有减小, 温升稍有上升. 因此, 对风扇电机来说, 当采用阻抗保护时, 若堵转温度超过标准, 可考虑改用细一档的线, 往往能解决问题, 而对转速风量的影响是很小的.定子漏抗包括槽漏抗xs, 端部漏抗xe, 谐波漏抗xδ及磁桥漏抗xb,它们的增大将引起最大转矩的减小, 而罩极电机为了充分利用其工作可靠的特点往往将额定工作点安排在最大转矩附近(尤其是风扇用电机), 其中以xb增大, 会使高速段转矩明显下降, 比其余漏抗更为不利. 因此一定要控制磁桥的厚度, 决不可太厚, 导致漏磁过大。
6.5 转子电阻r2
气隙磁场为圆形与椭圆时, r2的大小对转矩的影响是不一样的, 在对称电机中, 气隙为圆形旋转磁场, r2增大时, Tmax的转差率增大, 而Tmax值不变, 中速区凹下减小, Tst增大. 在罩极电机中, 各绕组的磁势不能满足圆型磁场的三个条件, 因此总存在负序分量. 当r2变化时, 正序转矩和负序转矩分别按对称电机T-n曲线变化规律, 从而其合成转矩, 当r2增大时不但Tmax的转差率增大, 凹下减小, 而且Tmax值减小, 而Tst却变很小, 这种情况可由图5说明。
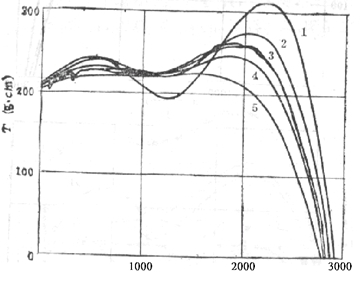
图5 转子电阻对机械特性的影响 (电阻随序号增大)
事实上, Tst与r2之间有一个最佳值, r2在某一值时Tst将获得最大值. 因此, 罩极电机还是尽量减小r2为好, 以求大的输出. 不过当电机采用抽调速的话, 降速时整条T-n曲线要下降, 就有可能使电机陷入低速爬行, 到不了应有的稳定转速。
在几瓦的小电机中, 应尽量采用少槽浅槽转子, 这对稳定铸铝质是大有好处的, 因为冲片本来很小, 槽一多, 每槽面积就小, 再若槽深一点, 则尤其槽底部易出现打不足现象, 甚至断排, 造成电机质量波动。
6.6 气隙长度δ
对异步电机而言, 从正弦波时的理论分析可知, δ应尽可能小, 因为δ小, 激磁电抗增大, 从而激磁电流减小, 降低了空载电流, 使功率因子上升、 效率提高。但是δ小了, 精加工精度要求高, 易造成偏心值(相对值)增加, 使制造和运行都增加困难。 另外, 气隙中并不是正弦波, δ小了, 谐波磁场及谐波漏抗增大, 导致Tst、Ist和Tmax减小, 并且谐波转矩和附加损耗增大, 造成较高温升和较大噪音。在罩极电机和其它单相电机中,δ取的比三相电机大一些是有好处的:
(a) δ大一些, 定转子谐波漏抗和转子斜槽漏抗减小, 其结果是Tst和Ist均增加, 由于Tst增和率大于Ist, 故δ适当大一些可改善电机的起动性能。而且由于Tmax与电机漏抗成正比, 故气隙增大, Tmax可提高。
(b) δ大一些, 减小了定、转子谐波磁通幅值, 由于杂散耗与谐波磁通幅值的平方成正比, 故大的δ可减小电机的杂散耗, 使效率稍有增加。当然, δ大了, 不仅空载电流增加、功率因子下降, 也使负载转差率有所下降(即转速有所上升), 负载电流也有所上升, 实际效率的增减要看哪一个因素为主导。
(c) δ大一些, 可使转子表面损耗下降, 从而转子表面发热大为减小, 向定子辐射热量减小, 故温升应下降. 但若δ加大过多, 将使气隙所需磁势增加, 这势必由增大输入电流来补充, 从而使电机饱和程度增加, 铜耗增加, 温升反而上升。
(d) δ大一些, 即使气隙的实际偏心值不变, 其相对值(气隙不均匀度)小了, 这在单相电机中尤为重要. 因为气隙不均匀度将导致单相电机在不同转子位置有不同的起动转矩, 而减小气隙不均匀度将减小Tst的波动. 而且由于δ加大削弱了高次谐波, 使附加转矩减小, 从而电机的Tmin增加, 即T-n曲线中速区的凹下减小。
(e) 由于任意两个谐波磁场相至作用产生的径向力约与δ2成正比, 故δ大一些可降低噪音及减小振动. 理论分析可知, 当气隙由δ1改变为δ2时, 相应的电磁噪声级弯化近似为L1-L2=10 lg(δ2/δ1)4dB, 当然, 由于空载电流增大等原因, 实际中小于上式计算值。
基于上述原因, 在单相电机中, 气隙值一般要比三相电机大0.05~0.1mm, 一般情况下, 使用滚珠轴承时, 取0.25~0.35mm, 而使用滑动轴承时, 由于更易产生偏心的缘故, δ增加10%~20%, 对于罩极电机, 由于气隙中的谐波成分更严重, 故δ更应大一些, 尤其是方形电机, 多采用支架形式, 更易造成偏心, 故其δ常取到0.35~0.45 mm。
7.罩极电机主要尺寸及性能确定:
7.1 效率及功率因子初值:0.05~0.12 ( 0.2~10瓦 ),0.10~0.26 ( 10~100瓦 )
其中: η’─效率
COSψ’─功率因子
7.2 电机常数:
其中: CA──电机常数
Dil─定子内径(cm)
l─铁芯长度(cm)
n─转速(转/分)
7.3 长度直径比:
7.4计算长度:
(厘米)
7.5定子内径:
(厘米)
7.6气隙长度δ=0.025~0.05(厘米)
7.7极距:
(厘米) 其中 P──极数
7.8极弧长度:
(厘米) 其中: 
7.9转子外径:
(厘米)
7.10转子内径(轴孔):dB=(0.18~0.24)D2(厘米)
7.11转子槽数Z2按表1选取:
极数 转子槽数Z2
2 11,12,15,18
4 11,17,22,57
6 26,33
7.12转子斜槽角度计算:
斜槽角度= 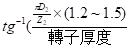
7.13定子槽满率 
其中: η──槽满率
dM──漆包线最大直径(mm)
WN──每极下绕组每槽匝数
S──电机定子槽率面积(mm2)
8.电机型号由产品代号、尺寸规格和额定电压代号三部分组成,具体如下:
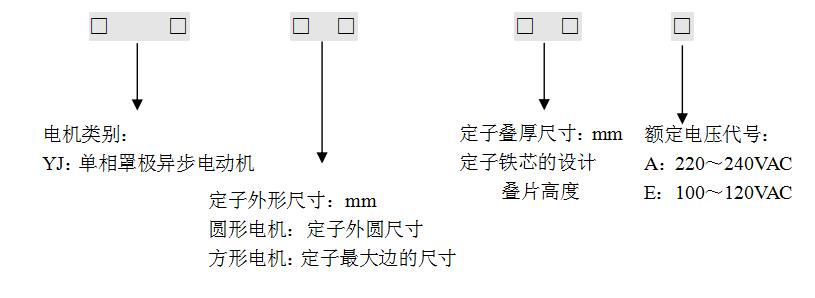